Understanding Injection Plastic Molds: A Game Changer for Businesses
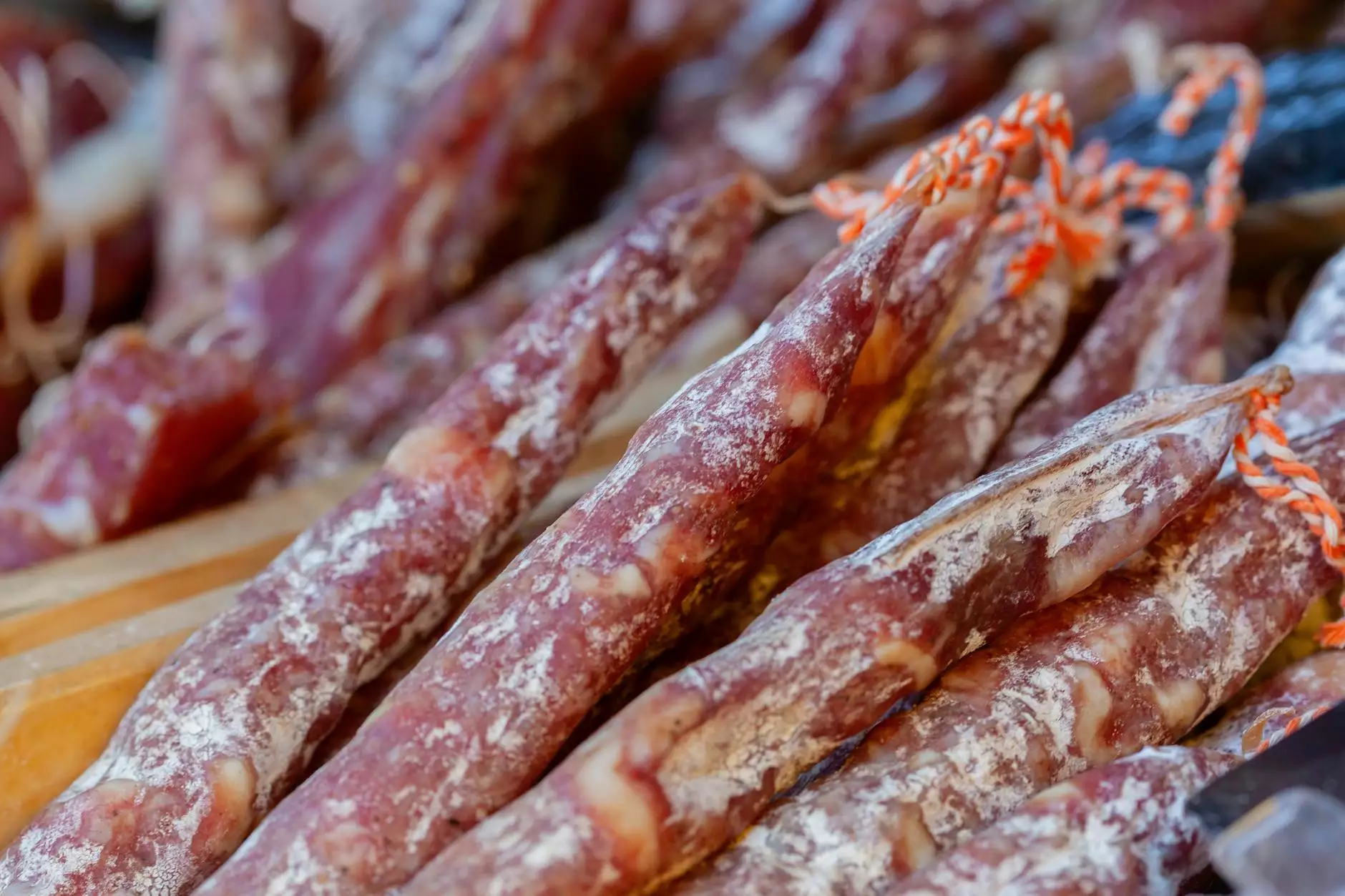
The world of manufacturing has evolved significantly over the years, and one of the most critical components that has driven this evolution is the use of injection plastic molds. These molds are essential in creating precise plastic parts that are widely used across various industries, from automotive to consumer goods. This article delves into the intricacies of injection plastic molds, their benefits, and how they can boost your business's efficiency and productivity.
What is an Injection Plastic Mold?
At its core, an injection plastic mold is a hollow metal block that is used to shape molten plastic into specific forms. During the injection molding process, plastic pellets are heated until they become liquid and then injected into the mold under high pressure. Once the plastic cools and solidifies, the mold is opened, and the finished product is ejected.
The Injection Molding Process
The injection molding process consists of several key stages:
- Material Selection: The first step involves choosing the right type of plastic material that meets the requirements of the final product. Common materials include ABS, Polycarbonate, and Nylon.
- Mold Design: The mold itself must be designed to facilitate the flow of plastic, cooling, and ejection of the finished product. Advanced CAD software is often used in this stage.
- Melting the Plastic: The selected plastic material is fed into a hopper and then melted in the injection molding machine.
- Injection: The molten plastic is injected into the mold under high pressure.
- Cooling: The injected plastic must cool adequately in the mold to take on its final shape.
- Ejecting the Product: Once cooled, the mold opens, and the finished product is ejected.
Types of Injection Molds
There are various types of injection molds, each tailored to specific needs and applications:
- Single Cavity Molds: These molds produce one part per cycle, ideal for low-volume production.
- Multi-Cavity Molds: Designed to create multiple identical parts in a single cycle, enhancing efficiency for medium to high-volume production.
- Stack Molds: These feature top and bottom cavities, allowing for two parts to be molded simultaneously, effectively doubling output.
- Family Molds: Ideal for producing different but related parts in one mold, which is useful for assemblies.
- Hot Runner Molds: These molds keep the plastic in a molten state, reducing waste by eliminating runner systems.
Benefits of Injection Plastic Molding
The use of injection plastic molding presents several advantages for businesses:
- High Efficiency: The process is highly automated, allowing for rapid production cycles and increased output.
- Precision and Consistency: Injection molds produce parts with incredible accuracy and uniformity, crucial for industries requiring strict tolerances.
- Material Versatility: A wide range of plastic materials can be used, making it adaptable to different project needs.
- Casting Complex Designs: Injection molding can create intricate shapes and designs that are difficult to achieve using other methods.
- Reduced Waste: Materials can be reused, and the process generates minimal waste compared to traditional manufacturing methods.
Injection Molding in Different Industries
The versatility of injection plastic molds allows their application across various industries:
Automotive Industry
In the automotive sector, injection molding plays a vital role in manufacturing parts such as dashboards, panels, and other interior components. The ability to produce lightweight yet durable parts contributes to improving fuel efficiency and vehicle performance.
Consumer Goods
Consumer products like containers, toys, and kitchenware benefit from the efficiency and precision of injection molding. This method allows for mass production of affordable items while maintaining a focus on quality.
Medical Devices
Injection molding is crucial in medical device manufacturing, where hygiene, precision, and regulatory compliance are paramount. Devices like syringes, inhalers, and surgical instruments rely on high-quality injection molded components.
Electronics
The electronics industry utilizes injection molding for producing housings, connectors, and other components. Given the rapid pace of technological advancement, the speed and flexibility of injection molding are indispensable.
Working with DeepMould.net
When it comes to metal fabrication and injection mold manufacturing, DeepMould.net stands out as a leader in the field. Our experience and commitment to quality ensure that we deliver exceptional injection plastic molds tailored to our client's specifications.
Quality Assurance
At DeepMould.net, we prioritize quality at every stage. Our rigorous testing and quality assurance processes ensure that every mold we produce meets the highest industry standards.
Customization and Expertise
We understand that each project is unique. Our team of experts works closely with you to design and manufacture molds that meet your specific requirements while maximizing efficiency and cost-effectiveness.
Advanced Technology
Utilizing the latest technology in injection molding and metal fabrication, we ensure that our manufacturing processes remain at the forefront of the industry. This commitment to innovation allows us to provide our customers with the best possible products and services.
Conclusion
The significance of injection plastic molds in modern-day manufacturing cannot be overstated. From functional components in the automotive industry to intricate designs in consumer goods, injection molding revolutionizes production. Partnering with experienced manufacturers like DeepMould.net can help businesses tap into the benefits of this powerful technology, driving efficiency, reducing costs, and achieving superior product quality.
As we move forward, staying updated with advances in injection molding technology and processes will be crucial for businesses aiming to remain competitive in an ever-evolving market.